①企画/打ち合わせ
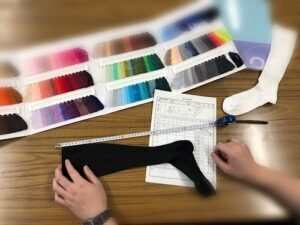
製品のデザインやコンセプトの決定
製品の仕様、素材の選定、寸法、機械ゲージ数など
(ベンチマークなどあればよりスムーズに)
②プログラム作成
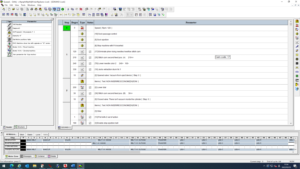
靴下製造機械専用ソフトを使用してプログラム作成
(完成したら靴下編機に読み込ませる)
③専用機械で編立

数種類ある靴下編機から製品の特徴に合う機械を決める
(パイル生地ソックス→パイル専用編機)
(繊細で高級感のある靴下→針数が多いハイゲージの編機)
機械に糸を立て編立
④先縫い
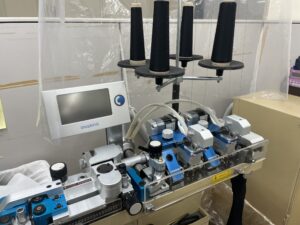
編立後の靴下のつま先を専用機械で縫製
靴下編機によっては自動リンキングも可能
⑤生地検査
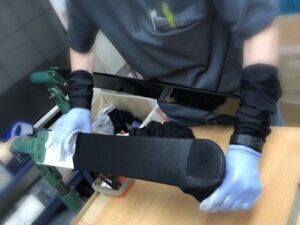
生地のチェック工程
ソックス用型板に靴下を通し両面検査
(針傷、糸抜け、不良個所等を入念に検査)
⑥セット
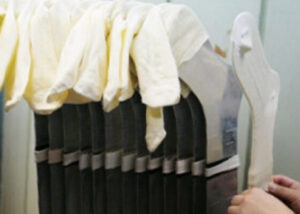
靴下を金属製の型板にはめて
セット機に入れ蒸気で成形する
(しわや形を整える)
⑦ペアリング
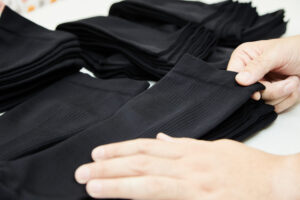
セット後の生地を同寸法の物とペアにする作業
(最終検品も兼ねて行う)
⑧包装/検針/箱詰
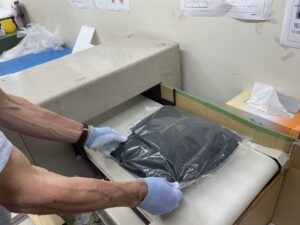
「包装」指定の資材
「検針」金属探知機で異物混入チェック
「箱詰」指定の資材
⑨完成

商品を出荷